Plastic extrusion for durable and low-weight components
Plastic extrusion for durable and low-weight components
Blog Article
Comprehending the Basics and Applications of Plastic Extrusion in Modern Production
In the realm of modern-day manufacturing, the strategy of plastic extrusion plays a critical duty - plastic extrusion. This intricate procedure, involving the melting and shaping of plastic through specialized passes away, is leveraged throughout different industries for the development of varied items. From car parts to consumer goods product packaging, the applications are vast, and the potential for sustainability is just as remarkable. Deciphering the principles of this procedure reveals real convenience and potential of plastic extrusion.
The Principles of Plastic Extrusion Refine
While it might show up complex, the basics of the plastic extrusion process are based upon reasonably straightforward concepts. It is a production procedure where plastic is melted and afterwards shaped into a constant profile via a die. The raw plastic product, commonly in the type of pellets, is fed right into an extruder. Inside the extruder, the plastic is subjected to warmth and stress, causing it to melt. The liquified plastic is then compelled through a shaped opening, known as a die, to form a long, constant product. The extruded product is cooled and after that reduced to the desired length. The plastic extrusion procedure is extensively utilized in various markets as a result of its adaptability, cost-effectiveness, and efficiency.
Various Kinds Of Plastic Extrusion Techniques
Building upon the standard understanding of the plastic extrusion process, it is essential to check out the various strategies included in this production method. In comparison, sheet extrusion creates huge, flat sheets of plastic, which are typically additional refined into items such as food product packaging, shower curtains, and car parts. Understanding these strategies is key to using plastic extrusion effectively in contemporary manufacturing.
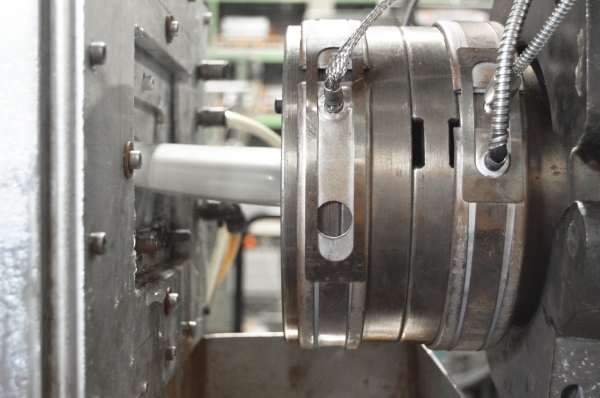
The Duty of Plastic Extrusion in the Automotive Industry
An overwhelming majority of components in modern-day vehicles are products of the plastic extrusion procedure. This procedure has actually changed the automotive sector, transforming it right into a more reliable, economical, and versatile production market. Plastic extrusion is largely made use of in the manufacturing of various vehicle parts such as bumpers, grills, door panels, and dashboard trim. The process supplies an uniform, regular outcome, allowing manufacturers to create high-volume get rid of wonderful accuracy and very little waste. The agility of the extruded plastic components adds to the total decrease in vehicle weight, enhancing fuel performance. The longevity view it now and resistance of these components to warm, cool, and influence boost the durability of automobiles. Therefore, plastic extrusion plays an essential role in automobile production.

Applications of Plastic Extrusion in Durable Goods Manufacturing
Past its considerable influence on the auto sector, plastic extrusion shows equally efficient in the realm of customer products making. This process is crucial in developing a large range of items, from food packaging to house home appliances, toys, and also clinical gadgets. The versatility of plastic extrusion enables makers to design and produce complex shapes and dimensions with high precision and performance. Due to the recyclability of several plastics, extruded parts can be recycled, decreasing waste and price (plastic extrusion). The flexibility, versatility, and cost-effectiveness of plastic extrusion make it a recommended choice for numerous durable goods producers, adding considerably to the sector's development and advancement. The environmental ramifications of this prevalent usage call for mindful consideration, a topic to be talked about better in the succeeding area.
Ecological Effect and Sustainability in Plastic Extrusion
The prevalent usage of plastic extrusion in making invites examination of its ecological implications. As a procedure that regularly uses non-biodegradable products, the environmental effect can be significant. Power usage, waste manufacturing, and carbon exhausts are all concerns. Nonetheless, industry advancements are raising sustainability. Efficient machinery minimizes energy use, while waste monitoring systems reuse scrap plastic, reducing raw material demands. In addition, the development of naturally degradable plastics provides a more other eco friendly option. In spite of these enhancements, further advancement is required to alleviate the environmental impact of plastic extrusion. As society leans in the direction of sustainability, makers have to adjust to remain feasible, stressing the importance of continuous research and improvement in this area.
Conclusion
In verdict, plastic extrusion plays a vital duty in modern production, specifically in the auto and durable goods industries. Its adaptability permits the production of a variety of parts with high accuracy. Its potential for reusing and advancement of naturally degradable products supplies an appealing opportunity towards sustainable methods, consequently dealing with ecological worries. Comprehending the basics of this process is vital to optimizing its benefits and applications.

The plastic extrusion process is extensively used in different markets due to its flexibility, efficiency, and cost-effectiveness.
Structure upon the standard understanding of the plastic extrusion process, it is required to check out the different techniques involved in this production technique. plastic extrusion. In contrast, sheet extrusion develops large, level sheets of plastic, which are commonly further processed into items such as food product investigate this site packaging, shower drapes, and cars and truck parts.An overwhelming majority of components in contemporary automobiles are products of the plastic extrusion procedure
Report this page